Łańcuch dostaw koncernu General Motors, którego częścią jest Isuzu Motors Polska Sp. z o.o. (ISPOL), stanowi rozbudowane, międzynarodowe środowisko. Ze względu na jego złożoność, zmian w modelu kooperacji w branży motoryzacyjnej trzeba dokonywać szczególnie ostrożnie.
Jednakże dzięki dobrze przemyślanym innowacjom, wspartym technologią informatyczną, możliwa jest optymalizacja istniejących procesów.
Fabryka silników w Tychach realizuje zakupy komponentów produkcyjnych u kilkudziesięciu stałych dostawców, głównie japońskich, ale także europejskich. Zamawianie odbywa się za pośrednictwem centrum dystrybucyjnego w Japonii (LSC – Logistics Service Company), które kompletuje dostawy od różnych kontrahentów, a następnie obsługuje ich wysyłkę do polskiej spółki.
Zakupy scentralizowane
Dotychczas cały proces zakupów był silnie scentralizowany – tyska fabryka składała zamówienia w centrum dystrybucyjnym. Centrum przekazywało zamówienia do poszczególnych dostawców.
Niestety, centralizacja procesu zakupów miała istotne wady. Po złożeniu zamówienia przez ISPOL brakowało informacji zwrotnej od dostawców o statusie zamówienia. Zdarzało się, że dostawca miał kłopoty z dostarczeniem do LSC zamówionej ilości zamawianego towaru i/lub realizacji dostawy na czas.
O niekompletności dostawy pracownicy fabryki z Tych dowiadywali się zwykle dopiero w momencie nadejścia informacji o dostawie. Zaburzało to proces planowania produkcji i obniżało zdolność fabryki do reakcji na zapotrzebowanie klientów.
Decentralizacja modelu zamawiania
W celu usprawnienia łańcucha logistycznego i minimalizacji niebezpieczeństwa zakłóceń dostaw, w ISPOLu podjęto decyzję o decentralizacji procesu obsługi zamówień. W tym celu dotychczasowe procesy biznesowe zostały zreorganizowane i na nowo zamodelowane. Obecnie polska spółka przesyła zamówienia bezpośrednio do dostawców, a japońskie centrum dystrybucyjne pełni jedynie rolę centrum/koordynatora logistycznego.
Nowy model biznesowy, po zmianach funkcjonalnych dokonanych przez BCC (aktualnie All for One Poland), jest wspierany przez użytkowany w ISPOLu system SAP R/3 w wersji 4.6c.
Teraz wszystko w systemie SAP
Do tej pory wymiana informacji pomiędzy systemem SAP R/3 w ISPOLu, a LSC, była ograniczona do trzech zbiorczych (dla wszystkich japońskich dostawców) typów komunikatów IDoc: zamówienie, potwierdzenie zamówienia oraz dostawa przychodząca.
W nowym modelu proces obsługiwany przez system SAP został rozszerzony o mechanizm planów odbiorów oraz potwierdzenia przyjęć materiałów.
Przede wszystkim konieczna była jednak reorganizacja procesów biznesowych w gospodarce materiałowej, oraz schematu komunikacji, w której obecnie uczestniczą zarówno producenci, jak i centrum dystrybucyjne (zarówno jako dostawcy, jak i odbiorcy informacji).
Komunikacja z dostawcami odbywa się za pośrednictwem wyspecjalizowanego portalu internetowego. Portal stanowi platformę wymiany informacji dotyczących ISPOLu (oraz innych fabryk General Motors), dostawców części oraz centrum dystrybucyjnego (LSC) odpowiedzialnego za transport.
Z systemu SAP R/3 wysyłane są dokumenty IDoc, które, po translacji do postaci XML, trafiają na portal, gdzie są udostępniane dostawcom. Jednocześnie kopia zamówienia w innym formacie trafia do LSC, na podstawie której LSC generuje tygodniowe plany dziennych odbiorów – PUS (Pick Up Sheet).
Na tej podstawie dostawcy tworzą dokumenty ASN (Advance Shipment Notification) stanowiące potwierdzenia ilości materiałów, które zostaną dostarczone w dostawie.
Uruchomione mechanizmy pozwalają na wielokrotne korygowanie tych ilości przez dostawcę. Dzięki temu, w przypadku niezdolności dostawcy do realizacji zamówienia w zakładanym czasie, czy zmiany ilości wysyłanych komponentów, informacja ta jest niemal od razu dostępna dla menadżerów ISPOLu.
Teraz osoby odpowiedzialne za logistykę fabryki posiadają narzędzie, pozwalające im na bieżąco dokonywać korekt w planie produkcji – w taki sposób, by nie miało to negatywnego wpływu na planową realizację zamówień dla klientów, czy plany produkcyjne.
Możliwość modyfikacji jest blokowana dopiero, gdy dostawca wysyła materiały do centrum logistycznego. Na tej podstawie LSC generuje dla ISPOLu zbiorczy komunikat dostawy, agregujący materiały od wszystkich dostawców.
Nowe rozwiązania BCC w EDI i HUM
W ramach zrealizowanych dla ISPOLu prac, BCC wykonało szereg rozszerzeń w systemie SAP R/3, które pozwalają na obsługę nowych komunikatów zamówień, przetwarzanie tygodniowych planów dostaw oraz generowanie z SAP R/3 zamówień bezpośrednio do portalu i udostępnianie dostawcom.
Dane o zamówieniu, przesyłane kanałem EDI w formie elektronicznego komunikatu IDoc, są wykorzystywane przez dostawców do przygotowania dostawy oraz do wystawienia faktury dla polskiej spółki. Następnie centrum dystrybucyjne kompletuje na podstawie tych danych dostawę dla ISPOLu
Do kompletacji dostawy używana jest funkcjonalność SAP R/3 o nazwie Handling Unit Management (HUM).
BCC przygotowało rozszerzenie standardowej funkcji obsługi dostaw przychodzących z HUM, które umożliwia obsługę dostawy z centrum dystrybucyjnego w referencji do dokumentów zamówień (wielu dostawców) za pomocą jednego dokumentu dostawy. Zaksięgowanie takiej zagregowanej dostawy powoduje wysłanie odpowiedniego komunikatu IDoc, niosącego informacje o potwierdzeniu dostarczonych ilości.
Dużym wyzwaniem przedsięwzięcia była rejestracja i przetwarzanie informacji o opakowaniach, ze względu na różnice w metodach identyfikacji opakowań stosowanych przez dostawców i centrum dystrybucyjne.
Dzięki mechanizmom, opracowanym przez BCC (aktualnie All for One Poland) wspólnie z przedstawicielami ISPOLu, wypracowano elastyczne i w pełni uniwersalne rozwiązanie tej kwestii.
O znaczeniu opisywanych zmian dla ISPOLu świadczy skala komunikacji elektronicznej. Zmodyfikowane rozwiązania obsługują kilkadziesiąt tysięcy dokumentów elektronicznych miesięcznie.
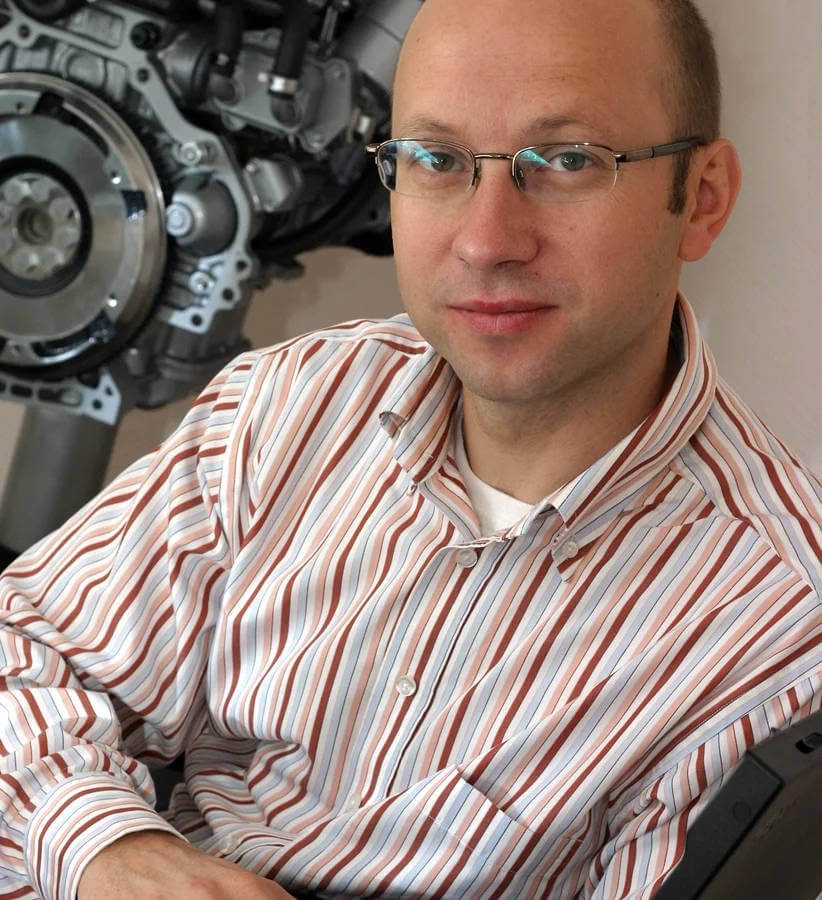
Jakub Borowczyk, Kierownik Działu Informatyki
Jakub Borowczyk, Kierownik Działu Informatyki tyskiej firmy, podsumowuje: „Dzięki zmianie w modelu zamawiania, oraz dokonanym przez BCC modyfikacjom w użytkowanych przez nas rozwiązaniach SAP, czynimy kolejny krok w usprawnieniu procesów logistycznych. Wykorzystanie danych z systemu SAP R/3 do komunikacji pomiędzy polską spółką, naszymi dostawcami i japońskim centrum dystrybucyjnym wpływa na usprawnienie współpracy. Automatyzacja oznacza znacznie mniej pracy z wprowadzaniem danych, a możliwość powstania błędów w dokumentach spada praktycznie do zera”.