Maintaining master data in the ERP system is a complex and difficult to manage process. This is due to both the data structure itself and also due to the need to engage a significant number of people with different competencies in it. Since master data management is not a major task, such as the execution of the production and purchases, it is often a process that is not given proper attention. This type of approach unfortunately has negative consequences during the operating work within the system. The quality of master data is, in fact, the determinant of the quality of major processes.
Master Data – Common Problems
Each day, production lines at the Lublin plant of Stock Polska release tens of thousands of bottles of flavoured alcohols and pure vodkas. The company produces alcohols intended for sale both on the Polish market and abroad. There are also special orders executed for retail chains. Such brands as Wódka Żołądkowa Gorzka or Stock Prestige are highly valued by customers.
From the SAP system point of view, Stock Polska has an assortment of more than three thousand material master records representing the finished products, semi-finished products, raw materials, packaging, and other materials. Before standardization and implementation of the master data management processes within the company, there were problems associated with a lack of a structured material master data maintenance process. The most important are: difficulties in entering data into the system on time; problems with collecting data; a significant risk of making a mistake when entering values into navigation fields; duplicates, etc.
SAP ERP in Stock Polska was launched in late 2010. During the implementation, the master data maintenance procedures were minimally developed and were veritably limited to information on what transactions should be used for specific activities. In particular, there was a lack of a process-based approach to master data management. It was not determined when and where to begin the process, who should do it, in what order, and who should pass what information to whom and when.
Master data maintenance was therefore realised as a series of actions performed on an ad hoc basis, based on phone and e-mail communication using the MS Excel forms developed during the implementation of the SAP system. A major problem was also the inability to determine, at any time, at what stage the entering of master data is, e.g. while introducing a new brand into the market. This lack of information caused difficulties in the coordination of activities aimed at developing master data.
The above-described problems with master data maintenance are a worry faced by a number of companies, especially for those where the material master file contains many items.
The IT Department of Stock Polska has initiated and subsequently implemented a project to introduce changes in this area, having in mind the importance of this issue, which causes great obstacles in daily work and additional costs. In February 2012 the company turned to BCC (now All for One Poland) for help to improve the master data management processes of materials in the SAP ERP system.
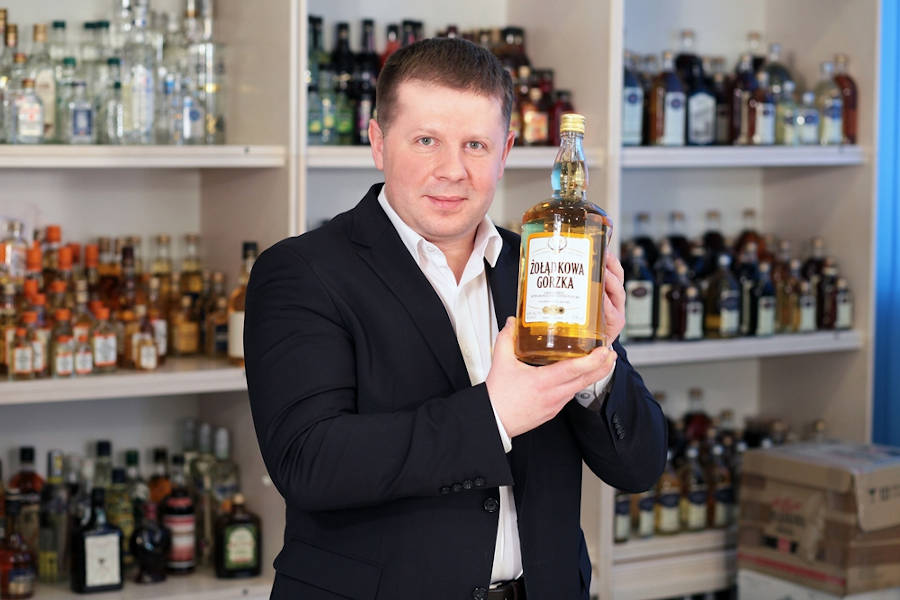
Marcin Lubawski, IT Director, Stock Polska
Improved Operational Efficiency
Standardization and implementation of master data management processes in the SAP system has had a positive effect on our operating efficiency, and has also removed the observed problems of “manual” work. I do not only have the IT Department in mind, but also the entire company. The role of the IT Department has certainly changed. Now we support the business, supervise the processes and assist in troubleshooting. It is worth mentioning that appropriately implemented processes with appropriate technological and organizational support leave more space to focus on the quality of work and its efficiency. They provide optimum comfort and motivation.
We started modelling the master data processes with the company BCC in February 2012. After completion of the analysis phase, we began implementation of the target solution. In January 2013, we successfully launched the materials section. We cared for the quality of the target solution and not only for the start-up deadline, and thus we spent almost a year working on this solution. It is very important to have well designed processes which are to be subsequently mapped in the system. Haste at this stage may result in errors at later stages of implementation and also in the solution itself. We still have to work on the processes related to suppliers. The existing cooperation with BCC has been carried out without reservation. The consultants have demonstrated the required knowledge and ability to cooperate at various levels of the organization.
Marcin Lubawski, IT Director, Stock Polska
Project – Assumptions – Aims
The aim of the project was to improve material master data management through the design of a process-based management model of such data and the implementation of an IT solution that will support the designed model from the system side.
The project was preceded by an analysis of the current situation (AS-IS), which highlighted the problems described above. Based on previous experiences in implementing similar projects, BCC from the very beginning, has recommended the use of the SAP Business Workflow technology as the best approach from a technical point of view. It was, therefore, assumed that there will be designed target process models (TO-BE) which will be implemented in the SAP ERP system in the form of the so-called workflow templates.
The high usefulness of SAP Business Workflow technology stems from the fact that it ensures automation of the execution of business processes (control of the sequences of activities and allocation of tasks to agents) and enables comprehensive tracking and auditing of the processes. The solution has been designed, implemented in the system and introduced. Since January this year, Stock Polska has been managing material master data in this new tool and according to a new process-based model.
Basic process – Circulation of the Material Requisition
The processes of creating material master data start when somewhere in the organization there is a need to create a new material in the system. Buyers of Stock Polska packaging need system representations of new bottles or cartons. Fluid technologists need the established representations of the macerates or raw materials used in the production process, such as flavours.
Needs always appear in different departments of companies. This situation is typical for most organizations. Therefore, an analogy with other processes was noticed, such as the organisation of non-stock account-assigned purchases (somewhere in the organization there is a need to purchase e.g. paper) or annual leave approval (an employee’s need to take annual leave). In these types of processes, all kinds of requisition forms are useful. For the non-stock account-assigned purchases, purchase requisitions in SAP ERP are often used. In the case of annual leave, leave request forms are used, etc.
Since it is similar to materials, a new system object was designed in Stock named ‘material requisition’. Of course, one could say that it would be enough to train members from different departments so that they can enter materials in SAP ERP directly. Such an approach, however, is not effective because users who need such data are experts in their fields but not in the field of master data. In addition, such decentralization would lead to inconsistencies (e.g., descriptions with lower or uppercase letters).
All kinds of requests are related to circulation processes. The request is created by an applicant and then sent to the approving user. The approver may then either approve or reject the request. If the request is approved, the applicant receives a notification of the approval, while if it is rejected, it goes back to the user in order to be withdrawn or corrected and re-submitted for approval.
A model of this basic process has been proposed by BCC to Stock Polska.
The approver in this case is the master data specialist. In Stock Polska, this role is performed by Bożena Teleńczuk-Kurowska, a Master Data SAP Senior Specialist who actively participated in the project and contributed to its success.
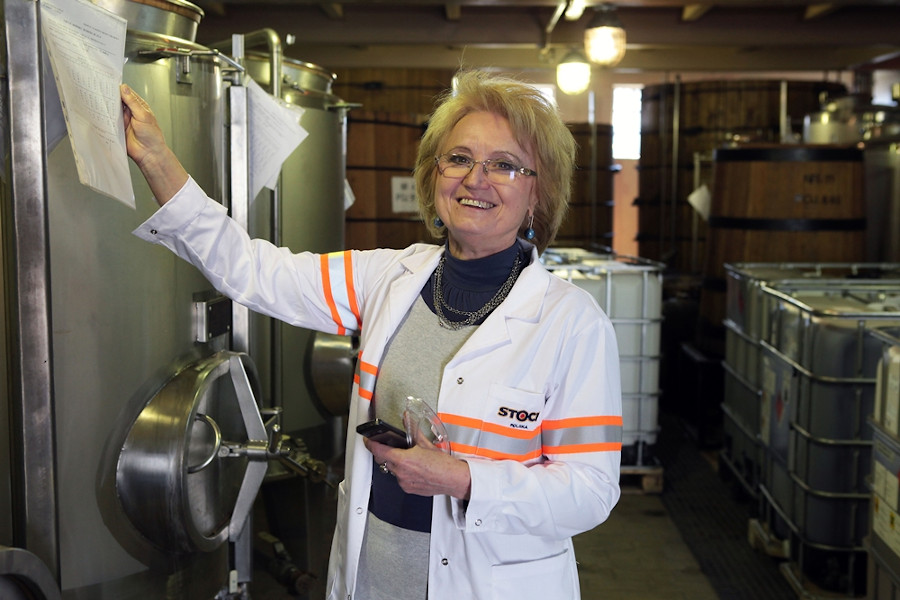
Bożena Teleńczuk-Kurowska, Senior SAP Master Data Specialist, Stock Polska
Quality, Comfort, Mobilization
From my point of view, one of the most important changes that occurred after the implementation of automatic maintenance of master data processes in SAP was the change to the working mode. A single position master data service in the IT Department was transformed into team work, carried out by one person or a group of people from different organizational units, responsible within the scope of the business for the data at every stage of the process.
For me, as a person managing the entire work related to master data, the tool has definitely raised the security of work in the company, and has also improved the comfort and quality. I can follow the progress of work on a regular basis – who accepted what data, and when– and I can easily verify and evaluate the activities of individual participants in the processes. The system itself organizes the work and queues the tasks. Thanks to its transparency, it highlights responsibility on a regular basis, and the results and consequences of particular peoples’ activities. Undoubtedly, it motivates the participants in the processes to carry out their tasks thoroughly.
This gives me a sense of security that all the data, after having gone through the standard validation path, is complete and factually impeccable, which directly translates into business continuity.
Bożena Teleńczuk-Kurowska, Senior SAP Master Data Specialist, Stock Polska
A mechanism was designed which, as part of a material requisition was to lead to the automatic creation of a real material master record in SAP ERP. It was also designed to cause the sending of new tasks to others involved in the preparation of the material to be used (e.g. to send a task to a technologist to a bill of material (BOM) for a buyer – entering the price list.)
Material Requisition – New SAP System Object
During conceptual work, how to implement the material requisition was considered. Is it to be an MS Excel format file or a system object in SAP ERP? Ultimately Stock Polska decided that the requisition should be implemented directly in the SAP system. The added value of such a solution is immense. The material requisition has the following functions and is characterized by the following attributes:
- It allows a need for new material to be registered (and allows changes to existing needs), as well as where this need originated from.
- The need is registered in a structured, systematic manner. The requisition is a new system document that receives a unique identification number.
- The user fills in the requisition in the best way they can i.e. they enter appropriate values in the fields. However, conveniently, the values do not need to be entered correctly (they are verified by a master data specialist). In addition, the values are not recorded in material tables such as MARA, MARC. They are recorded in a completely separate set of tables.
- When entering the requisition, it is possible to use three helpful mechanisms i.e. the material requisition gets filled with the values from the reference material master record, all fields have helpful information and tips, and the entered values are validated by the standard validation checking mechanism.
- The entire work on both sides: the requesting user has finished the material requisition (the basic process). The applicant, at some point, decides to release the requisition to the approver. The system automatically triggers an appropriate workflow process, depending on the type of material, and sends the requisition to the master data specialist’s workflow inbox. The specialist also works on the requisition form. After the verification/correction of the field values, they generate the material master record directly from the material requisition with a single click. There is no need to rewrite the contents of the requisition.
The material requisition consists of two data areas: the header and the details. The header specifies what kind of material to create (or what material to change), what data views are needed and on what organizational levels the data is to be created/changed. The details screen contains field values (see the screenshot below). Material requisitions can be reported and monitored with a non-standard ALV report. The report also allows the user to go to the standard workflow log associated with a given request, which can track the entire process.
Implemented Workflow Processes
The solution used for comprehensive management of materials in SAP ERP is not only used to efficiently create and change the material master records themselves. In Stock Polska finished products additionally require establishing bills of materials, rate routings, performing calculations, establishing cost collectors and the release of the standard price. Semi-finished products (liquids) have similar requirements, although instead of rate routings so-called master recipes are created and the cost collectors are not required. For packaging and raw materials there are established long-term quantity-based contracts.
The establishment of such data must often be done in a certain order, e.g. to perform the calculation of the finished product, it is necessary to have a production version linking the bill of material and the rate routing. The bill of material determines costs of components, and routings determine costs of the performed production operations. Such data is established by different groups of people. There is also additional data, such as WM control cycles, which, due to their structure, are always established in Stock Polska in the same way (automation possibility).
Therefore, for each type of material, a separate process has been designed, which begins after the basic process is executed, that is, at the time of creating the material master record on the basis of the previously described material requisition. In order to distinguish the material master records in the process of development from the ready and active ones, it has been determined that the status of the material will be used. Materials under development have the status “WF – under development” and active “AT – Active”.
The workflow process accomplishes the sending of tasks in the required sequences – by a given type of material – to identified experts. The sequencing between the tasks is maintained where it is needed. However, some parts of the tasks are sent concurrently, e.g. verification of the putaway and removal indicators for WM functionality are sent concurrently in relation to the tasks of creation of bills of material and rate routings, since such data is not dependant on each other. When the required additional data is processed, a master data specialist is given a task to activate the material. Once activated, e-mail messages with predefined content are sent to all parties interested in finishing the process.
The system reads the interested parties from a special distribution list, which varies depending on the type of material. The implemented solution also automatically performs several tasks in the background, such as extension of the material by the required storage locations, or creating the WM control cycles.
Master Data Project Card
During conceptual work, it was noticed that there is a certain superior level of managing the creation of master data in relation to the level of the “1 process = 1 developed material”. Material master records in Stock Polska are rarely created ad hoc. Normally the need to create new material master records and the associated additional data (e.g. BOMs, routings) results from a business venture having its source in a new product development process (e.g. marketing of new alcohol, new packaging, or new promotion kits) or, for example,. a Value Engineering process aimed at cost reduction.
As part of such a project, it is necessary to create a group of material master records representing: product, liquid, bottles, cartons, and raw materials. What types of materials are necessary depends on the nature of the project. For this reason, an additional tool that is used to manage material master data creation projects was designed and implemented – the ‘master data project card’.
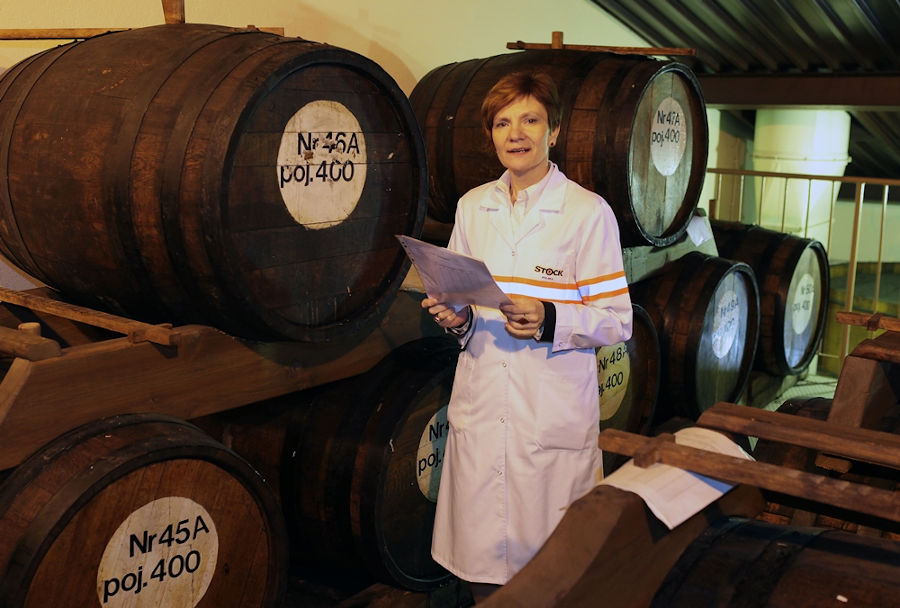
Joanna Dawidowicz, Chief Technologist, Stock Polska
The Superior Role of the Project Card
The project card constitutes a superior level of management when creating master data for us. It is an element that collects all the data associated with the implementation of a new product or change. Thanks to the project card, we know what sub-processes are required for the new project and who is responsible for them. At any given time, we can check at what stage of the project we currently are on, and if the work is carried out according to the schedule. In addition, the card is an excellent source of information about a given product and its individual elements.
The implementation of optimized data management processes has also resulted in measurable effects in the efficiency of collaboration between multiple departments within the organization.
Joanna Dawidowicz, Chief Technologist, Stock Polska
The master data project card is a system object that allows recording of projects to create material master data. Each project card contains a description of a project, the responsible Brand Manager, determines the type of project, and key schedule dates: completing data in SAP ERP, readiness of the plant for the production and the expected date of commencement of the sale. On the card it is also possible to enter long text explaining the project, or attachments, such as image files. The type of project is a specific parameter on the project card. It specifies what types of materials in a given project can be created and who is responsible for them.
The project card is usually established by the central marketing department (located in Warsaw) and then distributed (via the workflow mechanism) to the people responsible for the types of materials in the plant in Lublin. These people confirm their participation in the project and then submit material requisitions. In the material requisition there is a possibility to make a reference to the project card. Establishment of such a reference results in the fact that the workflow process, in which the requisition is being processed, is visible in the project card. This mechanism makes the project card a tool for collective monitoring of the work progress throughout the entire project, which requires the creation of a lot of new materials. Joanna Dawidowicz, Chief Technologist in Stock Polska, participated in creating the concept of the project card.
Towards Process Maturity
The company Stock Polska has made a significant investment in putting the master data management processes in order. The joint effort of the two companies – the team of business users from Stock Polska and BCC (now All for One Poland) – resulted in the designing, implementation and introduction of an advanced tool to effectively support the process-based approach to material master data management.
These types of projects help to increase process maturity of business enterprises. The material master data management process is no longer dependent on the heroism and rushing engagement of individuals in an impromptu process. Now, these processes are organized and managed with the use of an appropriate tool. An implemented process model, along with the tool based on the SAP Business Workflow technology, has definitely reduced the problems associated with material master data management. The work of end users has been improved thanks to the integrated tool. The use of the workflow mechanisms results in the processes becoming “visible” and auditable.
At any time we can answer questions such as: “At what stage is the process of adding the fluid for product A?”
Before the implementation, it was not exactly known how much time a particular process took. The analysis from the SAP Business Workflow engine in the production system of Stock Polska shows that 50% of the processes of creating master data of finished products on average last1 day 1 hour 3 minutes and 27 seconds. Obtaining such accurate information was not possible before.
Stock Polska/Polmos Lublin has been a part of the international Stock Spirits Group since 2007. It is a leader of pure and flavoured vodkas, and the largest producer of alcohol in Poland. The specialty of Stock Polska/Polmos Lublin is flavoured vodkas: Żołądkowa Gorzka (loosely, ‘bitter stomach vodka’), the Lubelskie family of vodkas (Cytrynówka, Żurawinówka, Wiśniówka); pure vodkas, (such as Czysta de Luxe, Stock Prestige, and Orkisz), and vodkas such as Żubr and 1906. A wide range of award-winning products in international competitions shows the unique position of the company in the Stock Spirits Group.
More information: www.stock-polska.pl