In October 2021, Delpharm and GSK announced the completion of Delpharm’s acquisition of GSK’s manufacturing plant in Poznań, along with all the infrastructure and the factory’s staff of about 700 people. For at least five years, Delpharm will continue to manufacture for GSK on a contractual basis, while GSK will remain the owner of the rights to the manufactured products and the responsible entity.
Delpharm plans to expand its global supply network. With a competitive cost base, high quality production, a focus on continuous development and the ability to produce a variety of pharmaceutical forms, the manufacturing plant in Poznań can make a significant contribution to achieving this goal. The main prerequisite for achieving these goals is an efficient and effective enterprise resource management system where business processes are carried out.
The previous owner’s manufacturing plants operate on the basis of an integrated SAP management system, in which all business processes are handled. It is a very extensive installation, covering the areas of finance and controlling, materials management, sales and distribution, production planning, plant maintenance management, quality management, warehouse management, document flow management and integration technologies (FI, CO, MM, SD, PP, PM, QM, WM, DMS, PI).
The IT policy assumes the widest possible use of the SAP standard and extensions, if any, with limited use of products from other vendors. The system has been developed for years and is perfectly tuned to the specific requirements of the industry. As a result, more than 90% of business processes are performed in SAP. In addition, the system is integrated with domain solutions used to operate precision equipment for weighing pharmaceutical ingredients and handling the movement of goods in the warehouse.
However, the contract for Delpharm’s purchase of the Poznań plant did not include the takeover of the SAP system, and the new owner faced a challenge – how to quickly deliver a system for the running plant so that it would continue to support all business processes without interruption. Under the terms of the contract, the plant could operate on the existing system until October 2022.
To this end, already at the stage of negotiations (early 2021), the company established cooperation with All for One Poland, expecting us to support it in analyzing the problem and providing a ready-made solution. The first phase of cooperation included the analysis of the situation, the identification of business needs and the preparation of an implementation concept and, on this basis, the valuation of the work.
After this stage, it was possible to move on to the second phase – the implementation and launch of the system.
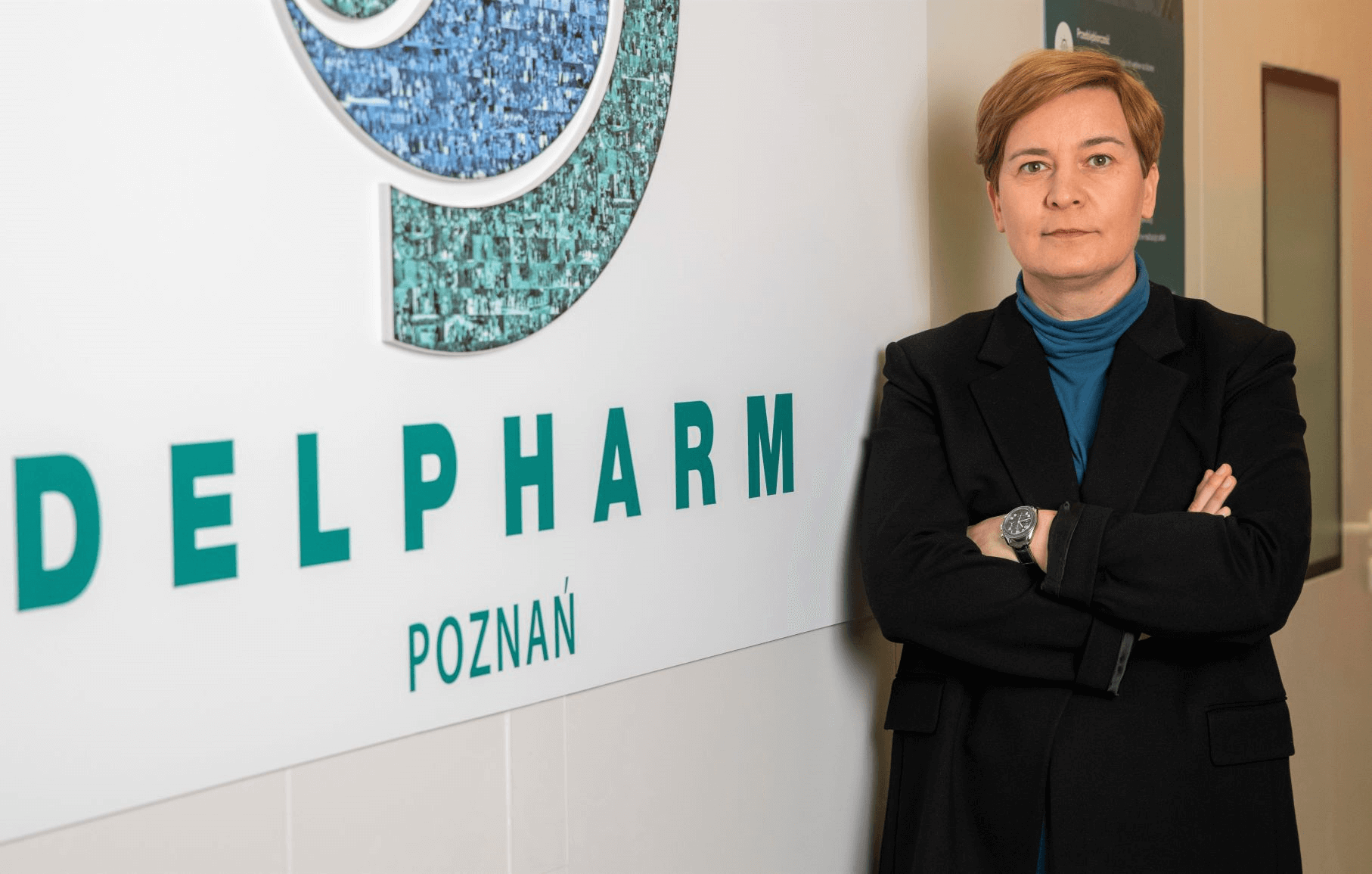
Kamila Sosnowska, Strategy Director, Board Member, Delpharm Poznań, Transformation Project Leader
Planning as a key to success
For our factory, the implementation of SAP was not a stand-alone change but part of a larger transformation program that included the transfer of ca. 100 applications of varying levels of complexity and involved changes to many processes that were transferred from MERP/SAP to other systems. On the technical side, the key, and at the same time the most difficult part of negotiating with the then current owner, turned out to be determining the approach to data transfer between the old and new systems.
In my opinion, the key to success was not only the very detailed transfer plan itself and the division of responsibilities, but also the plan of three test iterations arranged on an almost hourly basis, which allowed us to identify all kinds of problems and errors, which in turn ensured that the final data transfer at the last stage of the implementation went very smoothly and did not affect the final go live date. I think it’s also worth taking the time to establish rules for access to data that for various reasons will not or cannot be transferred to the new system, the so-called historical data, which in the case of our industry is a prerequisite for ongoing operations, and due to its volume and relations could not be transferred to the new SAP.
Remember that an implementation project is not just about the technicalities but also the soft, human side. It is extremely important to provide adequate resources and create an atmosphere in which team members do not feel left alone with challenges, difficult decisions or risks that arise every day. Clear communication about the future of employees after the project is completed is also vital. Regular meetings between managers and experts representing each module, and the support of the project leader, who struggles with the almost continuous assessment of risk of failing to meet the implementation deadline, especially at the final stage of the project, when the pressure and stress are already very high, are also important elements to guarantee the success of the project.
Kamila Sosnowska, Strategy Director, Board Member, Delpharm Poznań, Transformation Project Leader
Blueprint
In similar cases, a common solution is the SAP carve-out, i.e. separating the processes and data of a given entity from the source system (corporate solution) and transferring them to a new hardware platform. However, in this case, the previous owner did not agree to such a step. It was impossible to obtain a consent for third parties to access the current system and, as a result, the configuration and extensions could not be manually copied from the group system.
The only option available was to reimplement the system, i.e. recreate all functionalities and processes on the new platform based on the requirements provided by the business.
In the first step, all business processes (nearly 250) and extensions, including forms, reports and interfaces, etc., were mapped (more than 180). More than 80 master and transactional data objects were also identified as needed to be migrated. In addition, module concepts including configuration requirements were prepared for each module.
The analysis was completed in August 2021. Its result was a blueprint containing a complete concept and pricing for the reimplementation project.
The conclusion that was apparent at first glance: with a valuation of more than 3,500 project days on the integrator’s side and only a year for implementation, the time pressure would be one of the biggest project challenges (according to GSK’s declarations, the deadline in October 2022 could not be extended, after that date Delpharm would lose access to the SAP system of the previous plant owner).
Project
The project work began as early as September 2021. The schedule of tasks and activities was laid out in detail for each working week. At this stage, it was a challenge to coordinate the work of individual project teams. Over 45 consultants on the part of All for One and an equally large team of Delpharm employees participated in the work. Any delays in the implementation of the schedule entailed the risk of a domino effect and a delay in the go-live. And it should be emphasized that due to the volume of tasks, the schedule did not assume any time buffers. The key to success at the implementation stage was strict adherence to the delivery deadlines for each individual functionality and immediate verification of the solution by the client’s project team, culminating in feedback to the All For One team (fixes for identified bugs were delivered on an ongoing basis).
Consequently, the result of the implementation phase was a fully functional, pre-tested SAP system delivered as planned. An additional advantage of early involvement of the client’s team in the verification of the solution was the key users’ excellent knowledge of the new solution, which was of considerable importance for the testing phase.
In the pharmaceutical industry, validation of systems is required. This translates into a very high level of detail of test scenarios and extremely high documentation requirements. As a result, the testing stage is very labor-intensive and requires perfect team preparation, especially on the customer side. Delivering the solution on schedule, getting key users familiar with the new system already during implementation, and early identification and removal of most bugs allowed the team to focus exclusively on formal testing and validation activities. A small number of formal defects kept the workload for developing additional validation documentation at a low level. Ultimately, also this stage of the project was delivered on time in the vast majority.
The high level of competence and experience of the users had a significant impact on the smooth progress of the work and meeting the tight deadlines. Team members were excellent at defining their expectations, knew the terminology and the system, and were well versed in the implemented processes. The high motivation and commitment of people working on the project are also worth noting. Having learned from the experience of the SAP rollout project while still within the GSK structure – Delpharm employees were aware of how large and complex the project was, and imposed discipline on themselves both in terms of the temptations to expand the scope and to stick to the schedule.
The work was most intensive until April 2022. By July, we completed the system configuration phase in accordance with the concept.
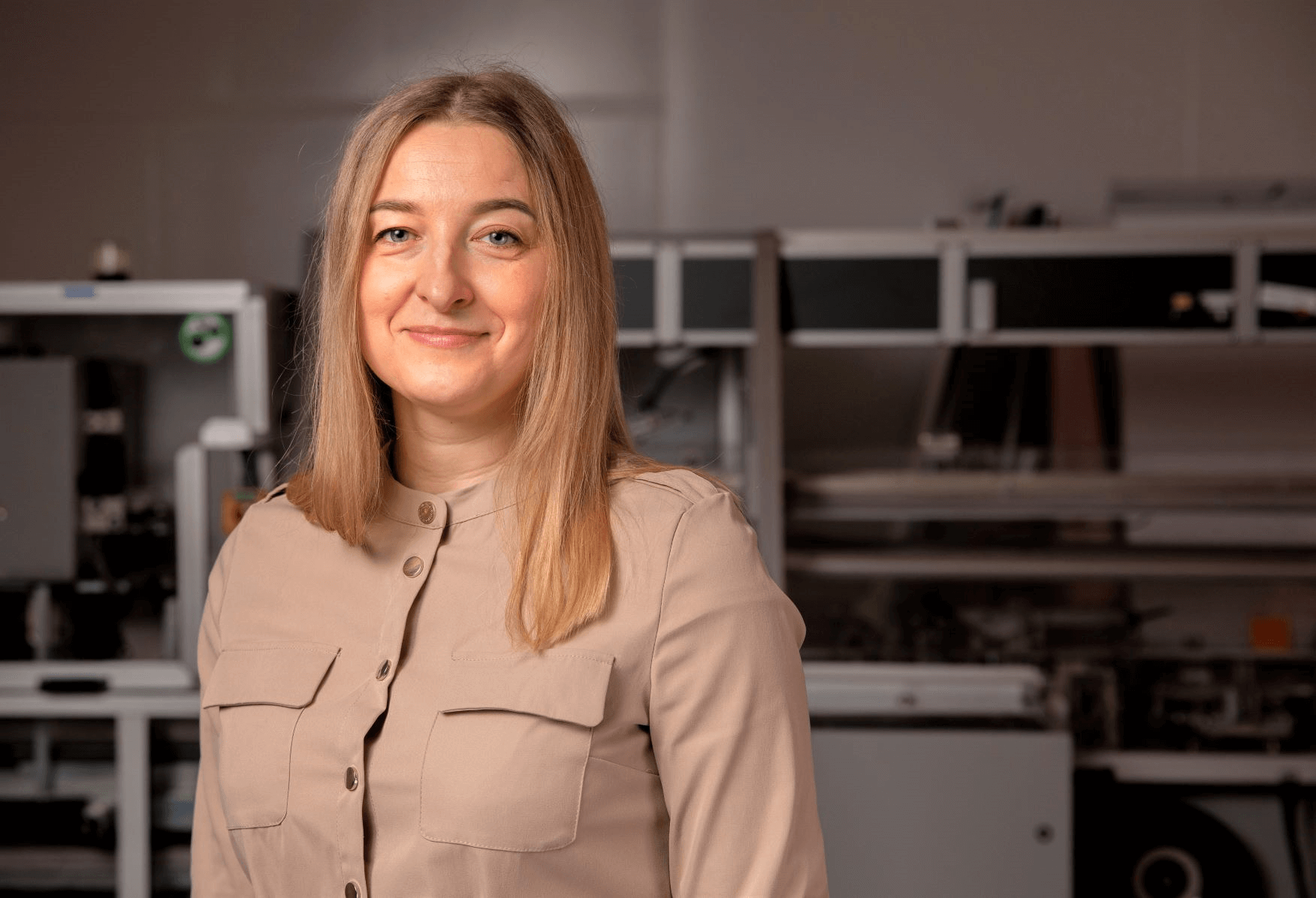
Anna Dobrzyńska-Gondek, Planning & Customer Service Manager, Delpharm Poznań, SAP Implementation Leader
Mature decisions
In addition to the obvious time pressure, the project was hampered by the fact that we had to guarantee formal validation of the system on the factory side, which requires additional documentation and a structured approach to testing. This forced us to execute several stages simultaneously, e.g. verifying data and preparing test documentation. During the transformation, the factory’s internal IT resources were dedicated to multiple applications and systems at the same time, so SAP was not the only priority during this period.
It wasn’t until the implementation and testing phase that we as users fully understood the importance of describing the solution specification in detail. Stating expectations in a too general way leaves a lot of room for interpretation, requires increased communication and can cause misunderstandings. It is important to be aware of this during the system planning stage.
In the FICO areas, where the way of working resulting from the change in the business model was most perceptible, additional changes could not be avoided during the implementation, however both parties showed the maturity and decisiveness to focus on the most critical ones.
The project was full of challenges, which, thanks to the commitment and professionalism of the implementing teams, were overcome and the project was successfully completed.
Anna Dobrzyńska-Gondek, Planning & Customer Service Manager, Delpharm Poznań, SAP Implementation Leader
Data migration and go live
In parallel to the implementation of the system, activities related to data migration were carried out. In this area, an additional risk factor was the involvement of a third party to the project, i.e. the previous owner, who undertook to extract and provide the master and transactional data.
In the systems of a highly regulated industry, the data that feeds them is critical (also subject to validation). For this reason, and because of the very high complexity and volume of data, All For One proposed three test migrations and a production migration as the fourth one.
The first iteration was based on small data samples but prepared for all facilities. It was mainly aimed at verifying the process itself, extraction, transformation and loading of data (verification of the prepared tools).
The second iteration already involved loading the full data set for all objects. At this stage, the team focused primarily on identifying problems related to the data itself (identifying variants of data previously unforeseen and adjusting the tools to process them).
The final test iteration was intended to definitively confirm the correctness of the entire process and allow an estimate of the total time required to transfer data from the old system to the new installation. This iteration was also the basis for conducting validation tests.
This approach proved to be extremely valuable – it helped identify the time dependencies between the various objects and to reorganize the entire data transfer process in such a way as to fit within the assumed time window.
More than a month was planned for the final stage of production data migration. During this time, the core data maintenance team on the GSK side performed successive extractions of defined data ranges and delivered them to Delpharm employees. They reviewed, cleaned and transformed them to an agreed template, and then handed them over to All for One consultants. Once the data was loaded into the system, the next step was testing to validate the migration.
Production migration of data involved shutting down the system and halting major business processes, including production. At Delpharm, staff vacations (September/October) and alternative activities, such as maintenance work and production line inspections, were scheduled during this time.
It was a big help that members of the project teams on the client’s side – as long-time users – were very familiar with the system, both the logic of SAP operations and the processes operating in the company. This made it possible to significantly reduce the entire training phase, focusing only on the modifications made to the original processes.
The go-live of the system took place as scheduled, in mid-October 2022. It ran smoothly, the few reported bugs were quickly resolved. After logging into the system, users started working in the new installation, however from their point of view, virtually nothing changed both in terms of process configuration and system performance.
The most important goal of the project has been achieved. The SAP system for the Delpharm plant in Poznań was recreated with its previous functionality, and the whole project was carried out according to a very tight schedule, with no delays.
Delpharm based in France, is among the leading global contract development and manufacturing organizations (CDMOs) for pharmaceutical companies. It has 18 plants offering most pharmaceutical dosage forms available on the market: tablets, ointments and soft capsules, ampoules and vials of injectable preparations, lyophilized products, suspensions and solutions. The company has been operating for more than 30 years and serves over 130 markets.