With 38 factories in Europe, both of the Americas and Asia, the Albéa Group – with headquarters in Paris – is an important player in the packaging market. Among its clients are the biggest manufacturers of cosmetics, body care products and pharmaceutical companies.
In Poland, Albéa has three manufacturing plants, among which is Albéa HPC from Łódź, specializing in the production of rigid packaging and caps for tubes, parts for cosmetic pumps, which are then delivered to other manufacturing plants in the group, as well as external customers.
SAP model, rollout program
Albéa Group uses the SAP ERP system, which supports all basic business processes. The developed system model supports the operation of the French headquarters and integrates production plants from around the globe into a single consistent tool.
Template SAP contains:
- a set of documented business rules for all business lines.
- configuration of processes for all business areas
- a complete set of ready-to-use reports and documents.
The consistency, maintenance, implementation of development works and system expansion is managed by an in-house IT/SAP team located in France, which, apart from design experience, also has complex programing expertise (ABAP).
The central IT team has been successfully realizing the project, which goal is to encompass all Albéa units with SAP ERP in the coming years.
In the middle of 2014, it was time for Albéa HPC Łódź, where a corporate rollout project for SAP solutions from the French headquarters began. The main goals of the project are:
- substituting the previously-used ERP system (Baan), which did not meet expectations (especially of reports) and in the near future could become a limitation for the development of local business,
- a consistent and unitary SAP ERP system supporting the fields of financing and controlling, material and warehouse management, production planning, as well as sale and distribution in the Łódź plant; ultimately the system will include all manufacturing plants in Poland, which will contribute to the development of business competence and management,
- the integration of HPC Łódź with other plants in the group, with which it will remain in close cooperation.
By using SAP ERP globally and conducting program rollouts, Albéa does not only have a well thought out concept of maintaining a business model (template) and the required expertise, but also has developed an original methodology and a detailed action plan, used in further projects.
In accordance with the best practices, the methodology defines the participants of the project, their roles and the relations between them. It describes the project phases, milestones and action procedures; it contains sample forms as well as other project tools. It also sets the communication rules – who, with whom, when… (e.g. the meeting of the steering committee takes place once a month, and those of the working teams every week, the project language is English).
Guarding the template
One of the most important assumptions of the rollout program is maintaining a consistency of the company’s SAP template as much as it is possible, and limiting discrepancies to a minimum. The above assumption also finds its reflection in the rollout methodology of Albéa, which is one of the basic tools in terms of maintaining consistency in the company. Its most important assumptions, that support this goal, include:
- aiming to eliminate the identified business disparities through adaptation and changes in the business processes of given plants (instead of changes in the system);
- only local deviations from the model are allowed, when it is necessary to adapt to national law, when there are processes in the local plant that do not occur in the model and cannot be forfeited and finally, when there are technical requirements behind this (interfaces, reports, documents, which are not in the template);
- engaging the local SAP partner into the project only after the approval of the fit & gap analysis.
The last point is largely the result of the fact that Albéa has at its disposal a complex team of SAP consultants, and partially because they want to further limit the amount of adaptations in the model, which could be proposed by an external partner. Such a model results in a faster actuation of the system in a plant. During the fit & gap analysis in HPC Łódź, previous rollout experience in other plants was used.
However, this does not mean that the partner has nothing to do in the project. By engaging an external company for rollout support, Albéa defines its role otherwise and puts it up against different tasks than traditionally in these types of projects. From the beginning, it is assumed that there should be large support of the project by local consultants in further phases of the project, which favors stability and predictability of the whole enterprise. Also in terms of an on-time start and the planned budget.
In the described project, the supporting partner of Albéa was BCC (now All for One Poland), of which the main responsibility concentrated on developing and conducting a training program for users, supporting users in the preparation of entry data and their migration to the system, preparing scenarios and test plans as well as supporting functional tests. Other tasks of BCC included preparing the functional specification, as well as working with Albéa SAP Factory (an internal team working on the development of the system) in the preparation of local solutions and their implementation.
Remaining in close direct contact with persons representing business departments of the Polish plant, BCC consultants intermediated in the communication with the SAP team in France – ‘’explaining’’ the logic of the IT system in a language that is understandable to the user, in the context of specific requirements and processes.
The next phase in which the role of the external partner is gaining importance is the preparation of the production start and supporting the start itself.
Investment in knowledge
One of the arguments for keeping the highest possible consistency of the system is the argument of savings – money as well as time that is “saved” in this way is invested by the company elsewhere – caring for a high competence of the users.
In rollout projects, it is rare for the training program to be so vast, well adapted to the needs of certain groups of users both in terms of scope specificity like in Albéa. A good understanding of the logic processes in the system, one’s role and responsibilities, as well as a free “movement” between successive screens form the basis for an effective work.
At the same time, gained lot was achieved –users were conversant with the system from the very start and quite easily accepted the new tools. It is very important because SAP – from their perspective – is much more demanding than the old application (the necessity to enter a much larger amount of data).
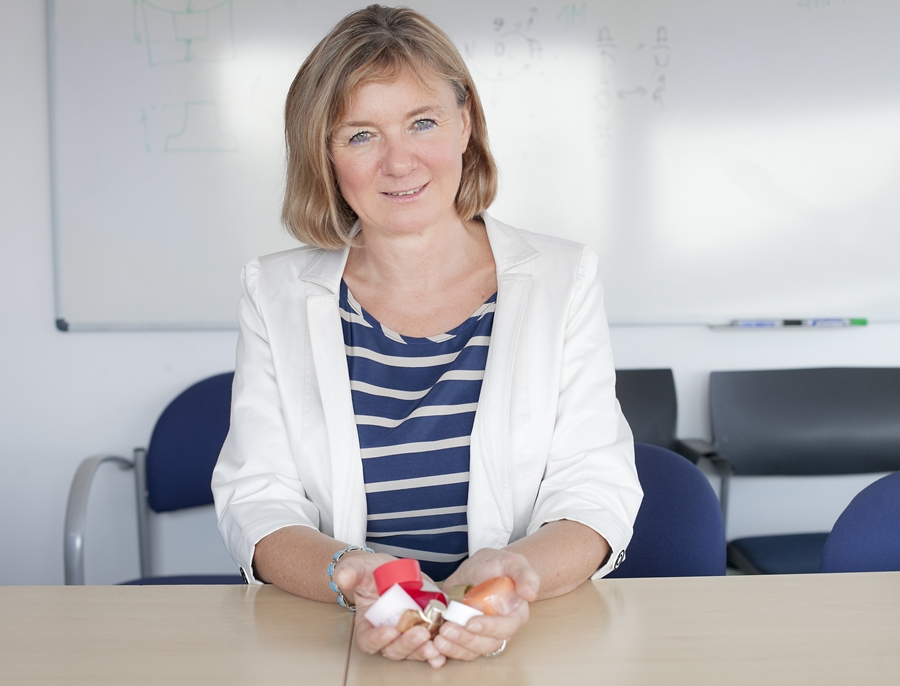
Małgorzata Mielcarek, KP, Customer Service & Supply Chain Manager, Albéa
A new perspective of management
SAP ERP in the first days after its introduction has shown us a company with a new perspective. In one place, we have readily available detailed information about the current situation in the range of production processes, sales, delivery realization, the planned and incurred expenditures, storage stocks and state of the finances. The planning occurs directly in SAP, from where the planners obtain all of the needed information, at the same time making sure that the information is up-to-date. We have eliminated Excel sheets from the planning process, which affects the process consistency.
In intercompany processes, we are observing a higher transparency, a faster data exchange with other plants in the group, including e.g. a better management of raw materials and production capacity. At the management level, this will translate into a more effective management and savings for the Albea Group.
For many employees of our plant, system users, working with SAP means additional responsibilities because the new tool is demanding in terms of the workload related to data entry. Additionally, we are also observing an increase in the effectiveness of work because SAP “repays” with better report information and supports actions as well as decision making in each stage.
I would also like to outline another benefit of the implementation. The large involvement of employees during the project resulted in a better teamwork and a better understanding of key processes. During project meetings, many people had the chance to see how their work impacts further steps in the process , what the data feed into the system is used for and which ones they found sometimes irrelevant before. I believe that the knowledge of one’s role and better understanding of the company also accounts for the increase in efficiency.
During the project, we were supported by SAP users from different plants of the group that already had experience in working with the system. It was especially valuable in the range of solutions dedicated and developed for the needs of Albéa in the corporate model.
Cooperation with BCC consultants was also very valuable. Especially during the system stabilization period and in the first days after the start. The presence of BCC consultants gave us a feeling of security and was a guarantee that the work will flow smoothly.
We were expecting a great deal of experience in SAP rollouts from the implementation partner. The knowledge of the conditions related to the maintenance and development of the systems in an international organization was important to us, as well as the knowledge of the local SAP specification. That is why we have chosen BCC (now All for One Poland).
A good project plan, involvement of all parties, as well as consistency in actions allowed us to realize assumptions and to start working with the system in a given time and budget.
Małgorzata Mielcarek, KP, Customer Service & Supply Chain Manager, Albéa
A “dry” start
Another assumption of the project methodology of Albéa is a “dry-run”. It is a start simulation, which takes into consideration all preparatory steps for starting a new system, with real storage inventory as well as migration and resource valuation. Such a “dry” start was performed at the turn of April and May and it allowed to identify typical, small errors, as well as larger ones that could not have been predicted beforehand (in all areas). In the case of the latter (for example, the necessity to consider additional changes in the model), there was time to think about the solution and to prepare it.
Between the simulated start and the real one, transactions were performed in parallel in both systems – the new one and the old one. It was a final test of competence for the user as well as the ability to further improve the data. Due to the high costs of the “double work”, companies rarely decide to undertake this step, despite the large benefits.
Investment in training as well as the dry-run phase are both important elements in minimalizing project risk and guaranteeing effective work in the first days after the start. Despite the fact that both of the elements are expensive, Albéa has estimated that the investments at a global scale recompenses a smooth incorporation of new departments into the system and an uninterrupted business operation.
Basic data
Another important aspect of the project was to prepare data for SAP: includingcustomers, suppliers, products, materials etc. Part of the data – after review and cleansing – could be migrated from the previous system. The less functionally advanced Baan had a smaller “appetite” and it did not gather some of the information required in SAP, so new structures had to be built for them.
In Albéa, the process of data preparation is taken seriously, emphasizing that it begins from the first day of the project and lasts practically to the start of the system.
The key users of the system were responsible for the quality of basic data, supported by users of the system from European plants of the group from the same business line (Tube), a different plant in Poland that is already using SAP as well as BCC consultants. Albéa uses its own tool for data migration, delivered along with the model.
In SAP since June
The system start in Albéa HPC in Łódź occurred at the beginning of June 2015.
The ability to report production costs and perform a profitability analysis was finally achieved in the FI/CO range, which was impossible in the previous system and required Excel sheets. The ledger, payables and receivables control, as well as asset management are further functionalities made available with SAP.
Customer service (in the SAP SD module) allows managing demand accounting for forecasts provided by customers in different formats. Order management also occurs in the system – from external clients and internal clients (using intercompany mechanisms). The abilities of the tools to manage prices are also widely used. The system also supports the processes of returns and credit control, as well as posting finished reports (including the order wallet, sales forecast list according to values, stock, deliveries, sales reports, and monthly sheet of invoices).
Subsequently, in the remaining areas of the supply chain (MM, WM, PP); the process realization occurs in SAP, in accordance with processes implemented in the corporation, taking into account the product specificity in the Łódź plant.
Cooperation: Mariusz Stawski, Bartosz Janowski, BCC Poland